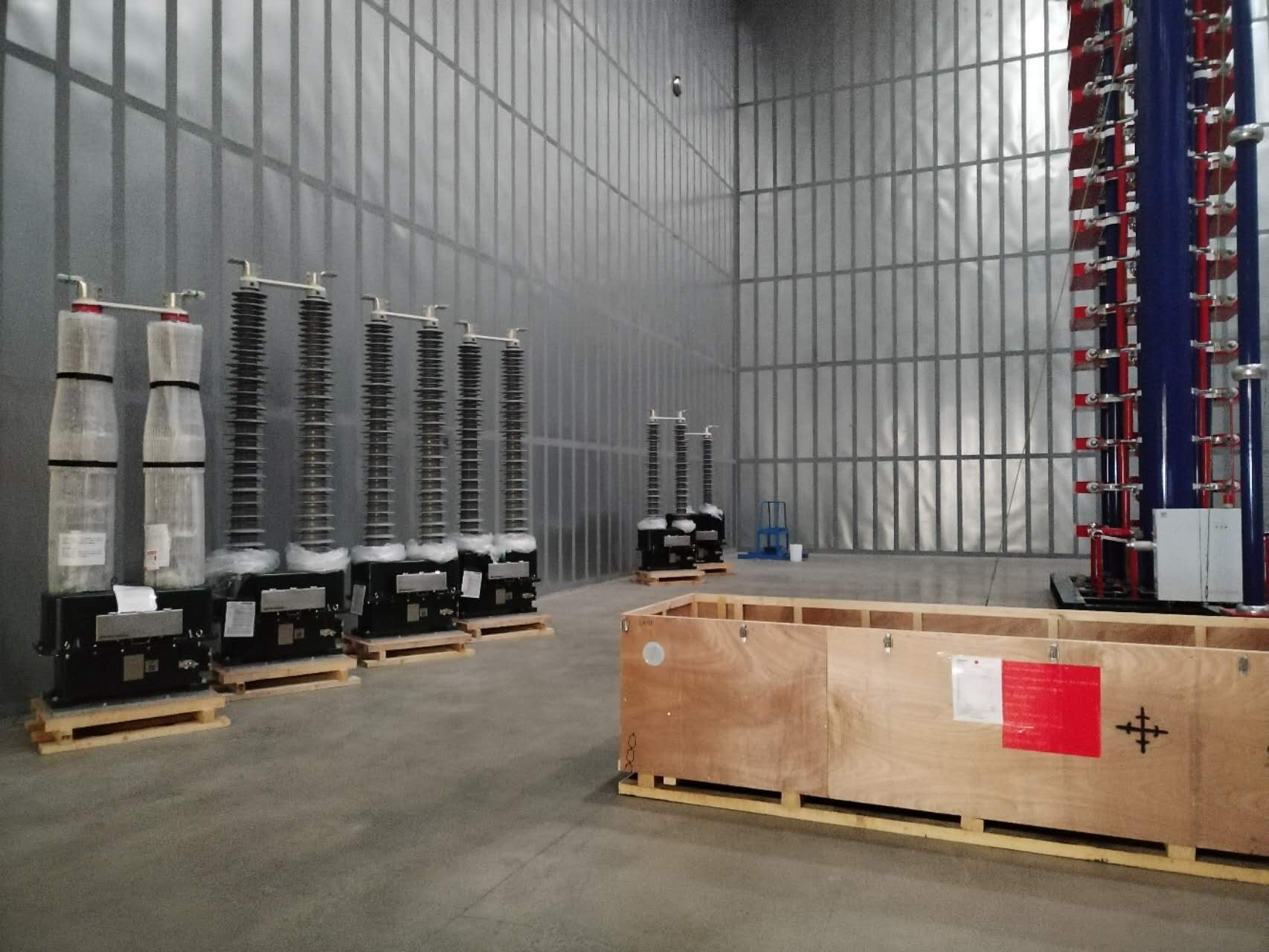
LRGBJ Dry Type Current Transformers Lined up in HV Test Lab
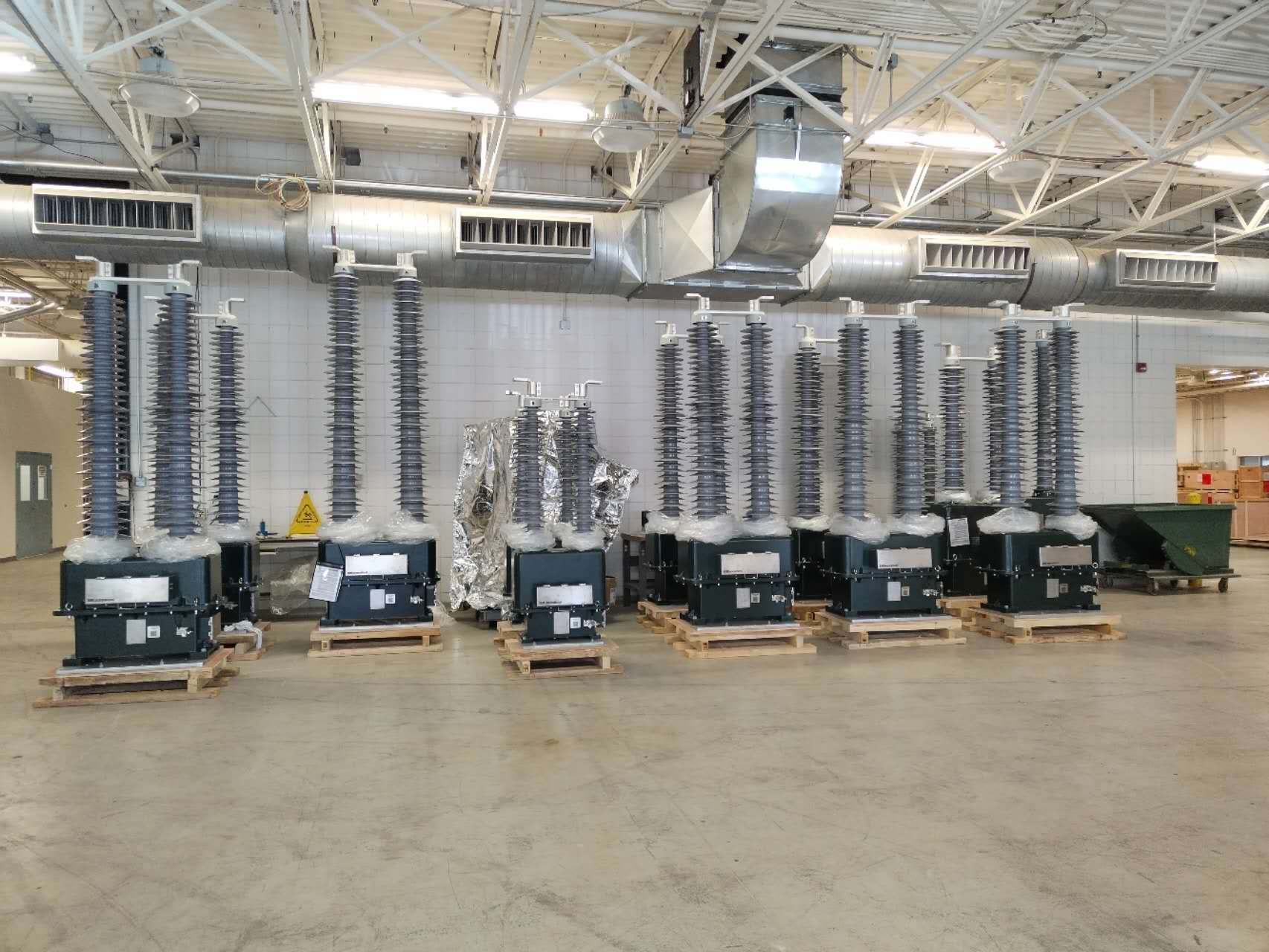
LRGBJ Dry Type Current Transformers Lined Outside the HV Test Lab
In early 2020 RHM International signed a long-term supply agreement with a major North American utility for the design, manufacturing and delivery of 10 different ratings of dry type HV current transformer for the utility’s 72.5 kV, 145 kV, 170 kV, 245 kV and 330 kV power grid requirements. Shortly after the award of the supply agreement RHM International received orders for a series of CTs of various ratings for new project requirements and replenishing the customer’s depleted inventory stock. As part of this supply agreement RHM International committed to performing the final qualification tests at its Hudson New Hampshire service facility. This arrangement allowed the customer convenient access for witnessing tests where 50% of the CTs being tested were required to be witnessed. With this quantity of CTs being received over a very compressed time period the Hudson team quickly realized that strict adherence to its processes for receiving, unpacking, inventory management, testing, re-packing and completion of the final documentation was going to be critical in order to meet the contractual delivery dates. A review of its operating processes was conducted in order to identify areas where efficiencies could be gained and the importance of accurate detailed test plans and the strict adherence to the test schedules was noted while recognizing the customer’s requirement for two weeks notification for tests to be witnessed.
Finally, to improve the efficiency of issuing the final test reports for the test program the Hudson team invested in the development of a software program to automatically generate the factory test reports from the test data files, thereby greatly improving the timeline needed to issue the final certified test reports for the test program.
The final qualification testing for this program was performed in accordance with IEEE C57.13 and CAN/CSA C60044-1 & 6 standards and the customer’s specification. These tests included:
- Verification of terminal markings,
- Verification of polarity,
- Measurement of insulation resistance,
- Breakdown voltage of the protective gap,
- Inter-turn overvoltage test,
- Power frequency withstand test for secondary windings and capacitive tap,
- Measurement of capacitance and dielectric dissipation (D.F.) factor before and after the power frequency withstand test,
- Lightning impulse withstand test (1 RFW and 5 FW),
- Power frequency withstand voltage test with Partial discharge for primary winding,
- Primary conductor resistance measurement,
- Tests for accuracy (metering and protection),
- Determination of secondary winding resistance (Rct),
- Determination of secondary excitation characteristic.
Where TPY accuracy class was specified, the following additional tests were performed:
- Steady state ratio error and phase displacement,
- Determination of peak instantaneous error,
- Determination of remanence factor (Kr),
- Calculation of secondary loop time constant (Ts) and transient dimensioning factor (Ktd).
This is an excellent example of how upfront planning and a dedicated work team can deliver a large quantity of final qualified HV current transformers while working under the pressures of a compressed timeline.
RHM International’s High Voltage Laboratory in Hudson New Hampshire was designed to perform mainly routine tests, type tests, as well R&D tests for RHM International’s manufactured products with nominal voltages up to 600kV, including but not limited to instrument transformers, bushings and cable terminations. The Hudson Test Laboratory is also available for contracted test services.