Most utilities today are operating with an aging transformer fleet that although significant may still have 10 to 20 years of life expectancy. However with these aging assets comes the problem of component reliability. To ensure that the transformers can meet their projected life expectancies money has to be spent replacing or refurbishing key components such as bushings and tapchangers. Transformer bushings, however, present the most significant risk to safety and reliability due to a number of factors some of which include:
- Government mandated phase out regulations for PCB contaminated equipment are forcing many utilities to retire many of their older station assets. Because of the age we are seeing with many transformer fleets still in operation the vintage style oil-filled bushings fall into a high risk category for PCB contamination (> 50 ppm PCB). Some utilities that oil sample their bushings are finding up to 25% of their transformer bushings and 35% of their oil circuit breaker bushings have PCB concentrations > 50 ppm.
- Problematic bushings due to oil leaks and elevated tanδ values. Oil leaks present an environmental concern with significant costs for clean-up and bushing repair or replacement. Elevated tanδ values is a predictor of insulation failure and the potential for a catastrophic failure.
- It is common knowledge that during a seismic event oil-filled bushings fail first leading to contamination and/or the risk of fire. Many utilities have embarked on replacement programs to improve the seismic resiliency of their older transformers by replacing the oil-filled bushings with new dry type silicon rubber housed bushings.
An example of the consequences of an oil-filled transformer bushing failure:
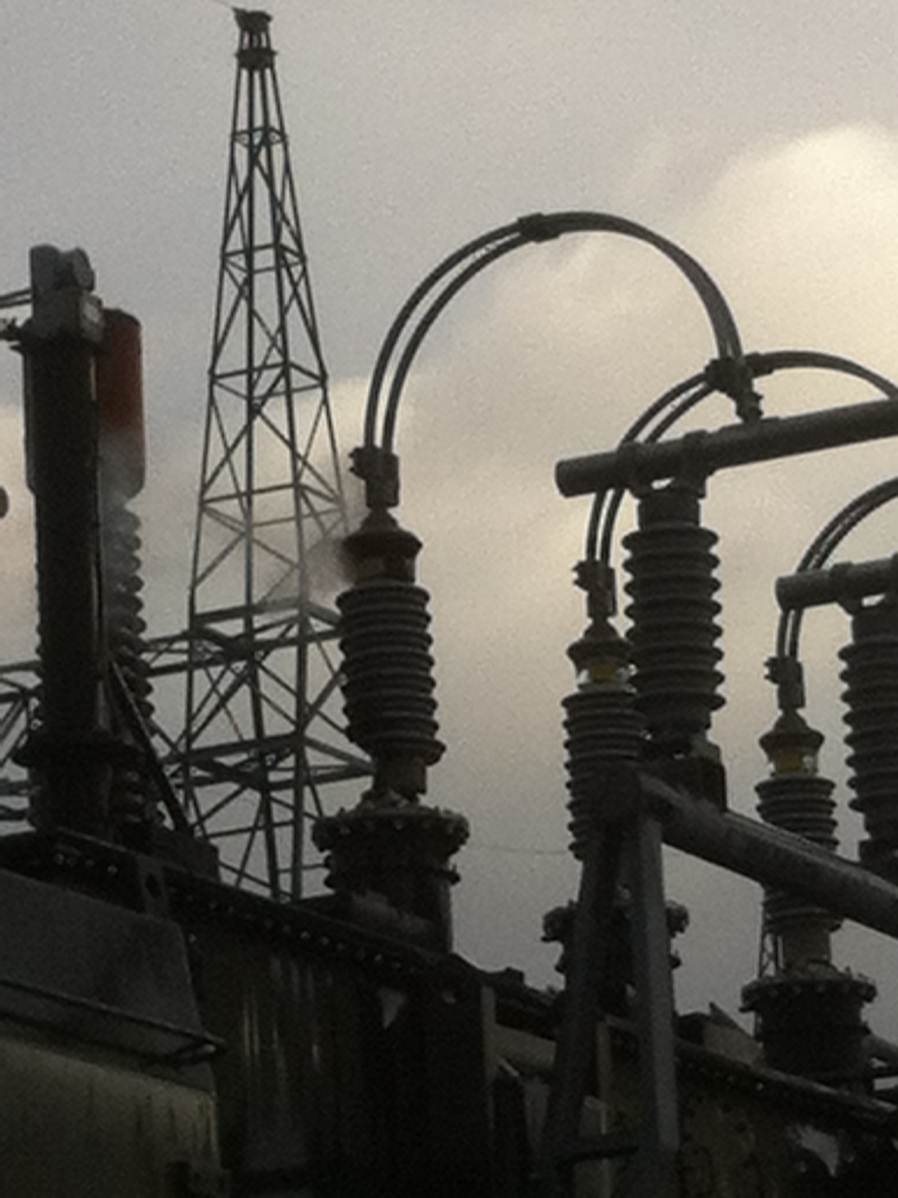
Bushing fails due to an internal fault which cracks the porcelain housing exposing the bushing’s internal paper insulation and oil
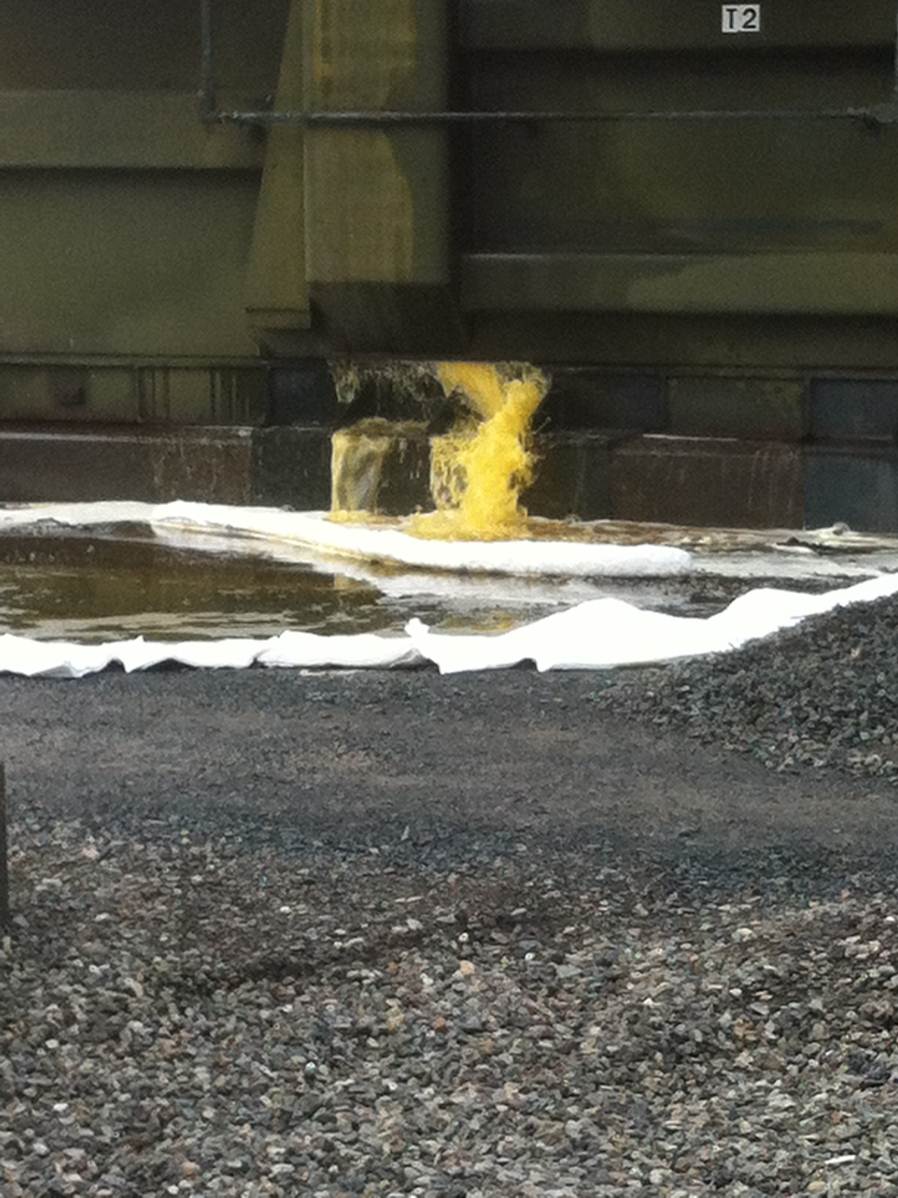
A subsequent line to ground fault causes a pressure wave inside the transformer tank which ruptures the bottom seal weld
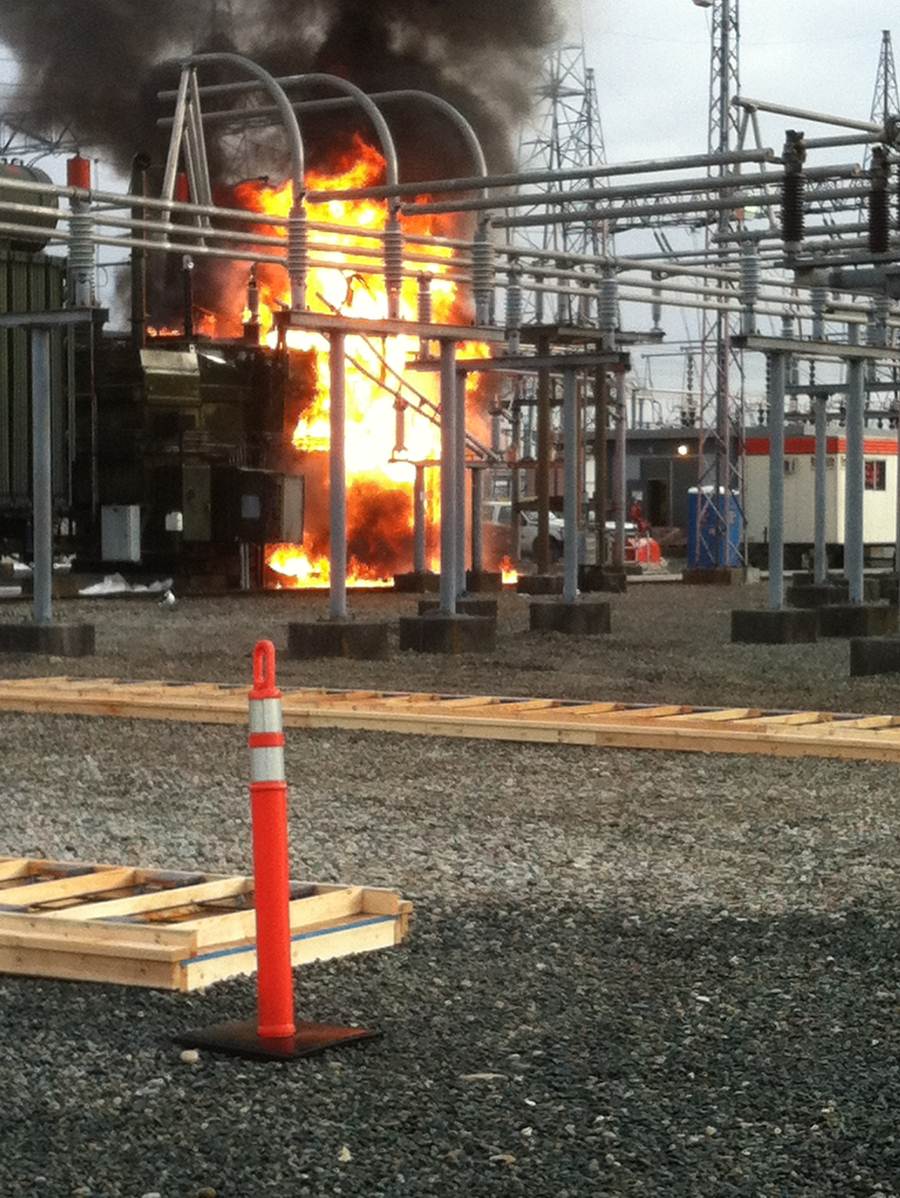
Burning material from the failed bushing ignites combustible gases that have formed inside the transformer tank
In consideration of these factors many utilities are implementing aggressive programs to change-out their older oil-filled bushings with new dry type bushings. When entering into such a program it is important to have a supplier that can provide:
- A dry type bushing technology that has a proven record under all types of extreme operating conditions.
- Timely customized bushing designs for your “like for like” replacements. Over the years industry standards have changed and trying to match the older dimensions with new industry standard bushings is very challenging.
- Quick lead times as the requirements for an annual bushing replacement program usually only get identified months before the scheduled field work.
When considering a dry type bushing technology for your replacement program you have a choice between two technologies: RIP and RIF®. The following differences between the two technologies should be considered when making your selection:
- The RIP insulation technology uses a creped insulating paper dried under temperature and vacuum and impregnated under vacuum with epoxy resin. The RIF® insulation technology uses no paper and is composed of fiberglass impregnated with epoxy resin wrapped between capacitance screens. The manufacturing process requires no vacuum drying and no vacuum impregnation which results in a simpler, less costly and faster manufacturing process.
- The partial discharge level and dissipation factor value of RIF® bushings are far lower than industry standard limits and remain stable over the operating life of the bushings. Bushings retested after 7 years of service showed the partial discharge, dielectric dissipation factor and capacitance to be exactly the same as the ex-works routine test results and in some cases to be better.
- RIF® bushings have proven to be extremely reliable with special lab tests showing that bushings with up to 25% of its insulation damaged (intentionally damaged for the test) were able to remain energized at its operating voltage up to 5 months before the test was stopped.
- The RIP technology requires special long term storage oil filled vessels for the oil end of the bushing. This is due to concerns about moisture ingress in the bushing’s paper insulation. The RIF® bushing requires no special storage conditions and can be left in their original crates until they are needed. It is not uncommon for outages to be cancelled and bushing replacement projects to be deferred so long term storage needs to be considered in your bushing procurement decisions.
In summary a bushing replacement program offers the utility a unique opportunity to upgrade the reliability of their transformers while improving the safety and environmental performance by replacing aging oil-filled bushings with the new dry technology type.
Download our technical brochures on RIF Transformer Bushings:
Brochure for IEEE Bushings
Brochure for IEC Bushings